Design for Additive Manufacturing Basics
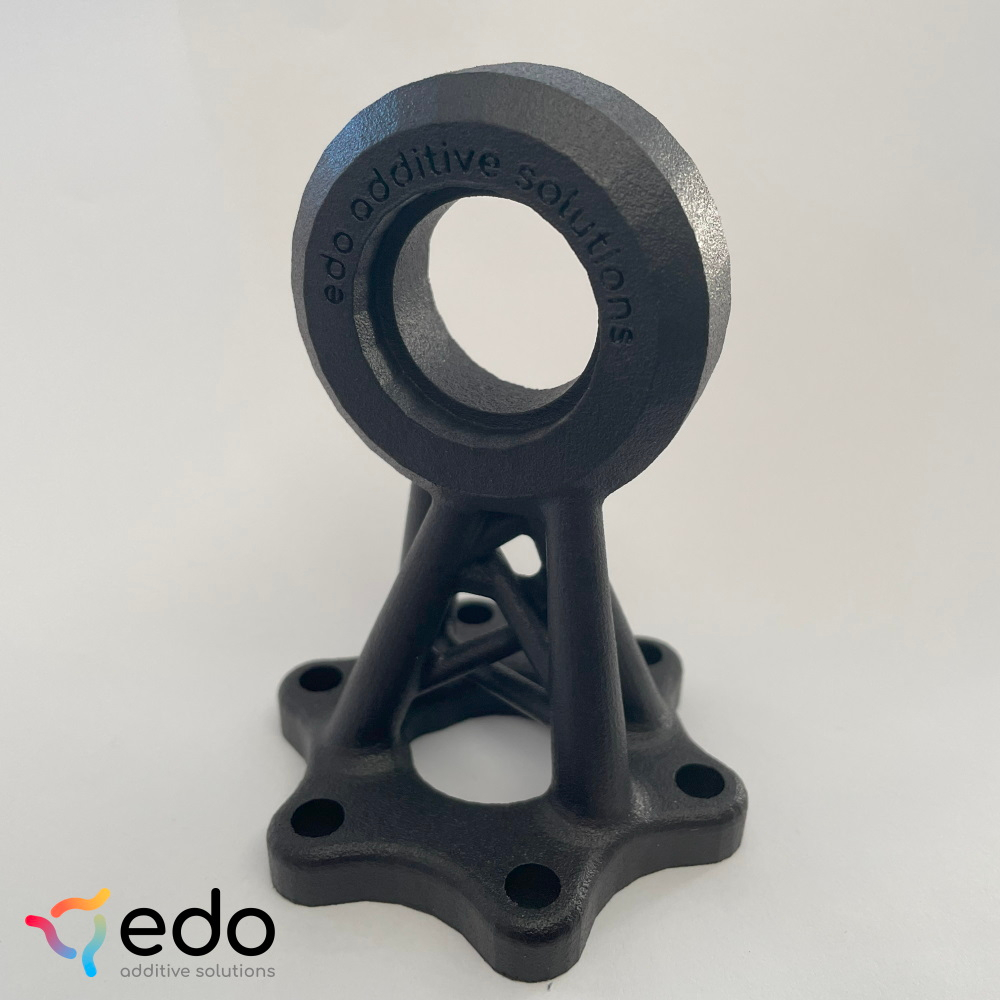
Introduction
In the realm of manufacturing, traditional methods have long dominated the landscape. However, with the advent of additive manufacturing (AM), a transformative shift has occurred, opening up new possibilities for design and production. Unlike subtractive manufacturing processes, which involve cutting away material to create a final product, AM builds objects layer by layer from the ground up. This revolutionary approach has given rise to a new set of design principles, collectively known as design for additive manufacturing. In this article, we will explore the basics of design for additive manufacturing and how it is reshaping the future of product development.
Layer by Layer: Understanding Additive Manufacturing
Additive manufacturing encompasses a variety of techniques, including 3D printing, stereolithography, and selective laser sintering, to name a few. Despite their differences, these methods share a common foundation: the layer-by-layer construction of objects. This process enables intricate designs that were once deemed impractical or impossible using traditional manufacturing methods.
Geometry Liberation: Complexity without Compromise
One of the primary advantages of design for additive manufacturing is the freedom it provides designers in shaping complex geometries. Traditional manufacturing methods often struggle with intricate designs, but AM excels at producing complex structures with ease. This geometric liberation allows for lightweight, high-performance components that were previously unattainable, unlocking a new era of innovation in industries ranging from aerospace to healthcare.
Material Selection and Optimization
Design for additive manufacturing also places a spotlight on material selection and optimization. Traditional manufacturing often relies on well-established materials, but AM opens the door to a broader range of possibilities. Designers can choose from various advanced materials, each with unique properties, to meet specific requirements. Additionally, design for additive manufacturing allows for optimising material usage, minimizing waste and enhancing sustainability.
Support Structures: A Critical Consideration
Despite its many benefits, AM comes with its own set of challenges. One crucial consideration is the need for support structures during the printing process. These structures provide stability for overhanging features but can be time-consuming to remove and may impact surface finish. Designers must carefully balance the need for support with the desired outcome, finding the optimal compromise between structural integrity and post-processing is essential since often the reason why 3D printed products are not cost-effective compared to traditional manufacturing is the excessive post-processing need arising from bad design and the consequent support needs.
Topology Optimization: Redefining Structural Efficiency
Another key aspect of design for additive manufacturing is topology optimization, a process that leverages advanced algorithms to design inherently more efficient structures. By analyzing the forces and stresses that a component will experience, topology optimization generates organic and lightweight designs, minimizing material usage while maintaining structural integrity. This approach is a departure from traditional design methods and exemplifies the paradigm shift brought about by AM.
Designing for Functionality: Beyond Aesthetics
In the design world for additive manufacturing, functionality takes precedence over aesthetics. While traditional manufacturing often involves designing for visual appeal, AM allows designers to prioritize functionality without sacrificing form. This shift in mindset encourages a holistic approach to product design, where each element enhances the final product’s overall performance.
Conclusion
Design for Additive Manufacturing is more than a set of guidelines; it is a philosophy that embraces the possibilities inherent in layer-by-layer construction. As AM continues to evolve, so will the design principles for additive manufacturing. By understanding and embracing these basics, designers can unlock a new realm of innovation, pushing the boundaries of what is possible in the world of manufacturing. The future is built layer by layer, and design for additive manufacturing is leading the way.
Do you need support in your designs? We are award-winning experts in design for additive manufacturing and can help you solve your problems. Just give us a call or write us an email, and we will find solutions tailored to your needs.
Call or write us here.
Weight and support optimized bracket for a robot
Subscribe to our newsletter to learn more about additive manufacturing.