Essential Design Rules for Mass 3D Printing
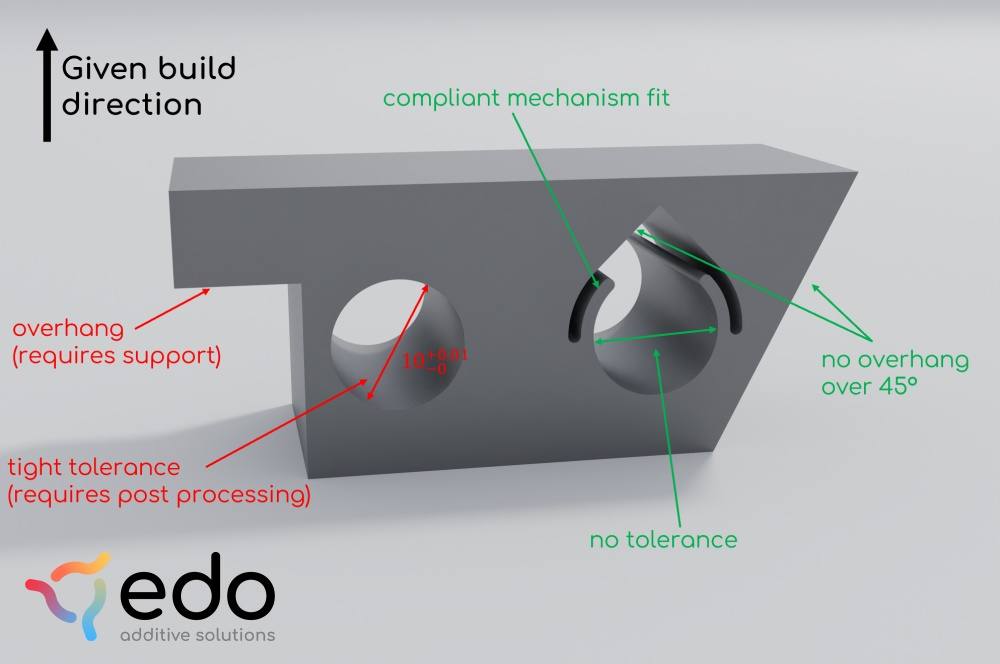
Introduction
Additive Manufacturing (AM) is a precious tool in the first two stages of a product life cycle (Development and Introduction) since it is very flexible for making prototypes. However, many companies struggle to use 3D printing in mass production. The reason is often the design of the part itself rather than the 3D printing process.
Since 3D printing has large design freedom, it’s possible to produce parts that are otherwise not manufacturable. However, this can also mean that some parts are not particularly suited for mass production on 3D printers. This can be due to that part needing a lot of post-processing (which might be fine if you only have a dozen of parts), or that it requires a very special machine. The building process can be slightly unstable which means that every batch is slightly different or even a significant amount of prints fail, which might not have been evident during the prototyping.
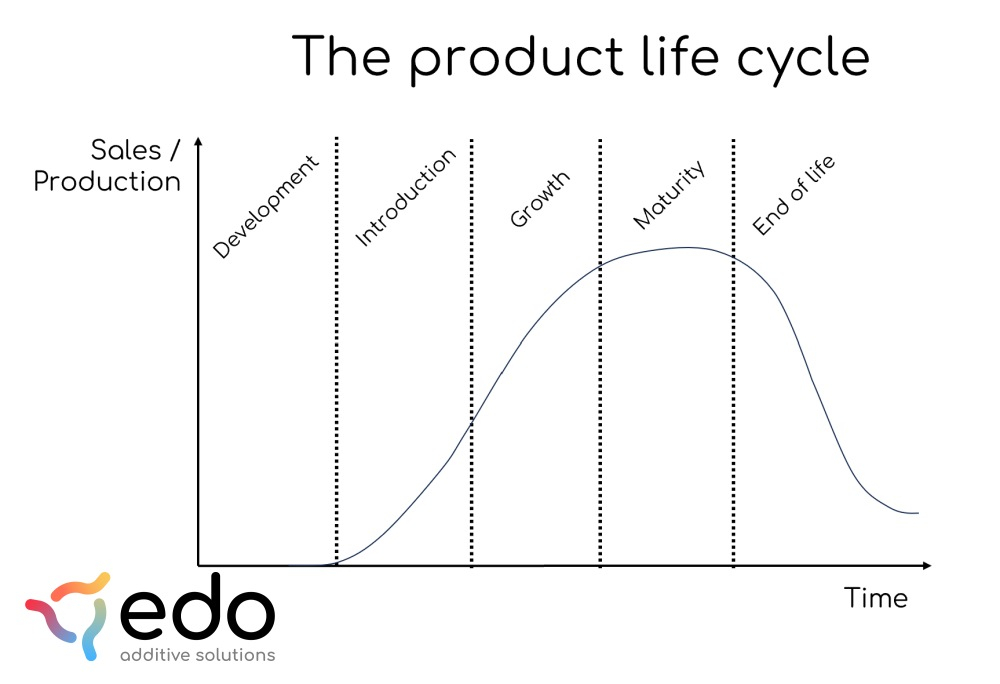
The product life cycle where 3D printing is mostly used in the beginning
There are hardly any universal design rules that apply to all 3D printing technologies because the differences between printing technologies are significant. However, we want to provide you with 6 “rules” which, in most cases, will help you keep your mass 3D printed parts cheap, reliable and high quality throughout all the batches and manufacturers you might have in the product life cycle.
1 Avoid too small features
Most 3D printing processes have a minimum feature size, usually between 0.05mm and 0.5mm. Staying above these minimum feature sizes is a must. However, not getting too close to those can help to reduce costs because small features are always at risk of getting out of spec. We usually recommend staying at least a factor of 2 above the minimum feature sizes if you need somewhat reliable tolerances.
2 Avoid overhangs
Most printing technologies can’t print horizontal overhangs without support structures. Support structures should be avoided as much as possible. Therefore, in general, avoiding overhangs over 45° will make parts more cost-effective since there is no need to remove that support. A great way to get rid of overhangs is making chamfers so that the build is gradually expanding. Some 3D printing technologies also have neat strategies like bridging in FDM 3D printing, where overhangs can be produced with only very little added material.
However there are also technologies like SLS, where this doesn’t apply.
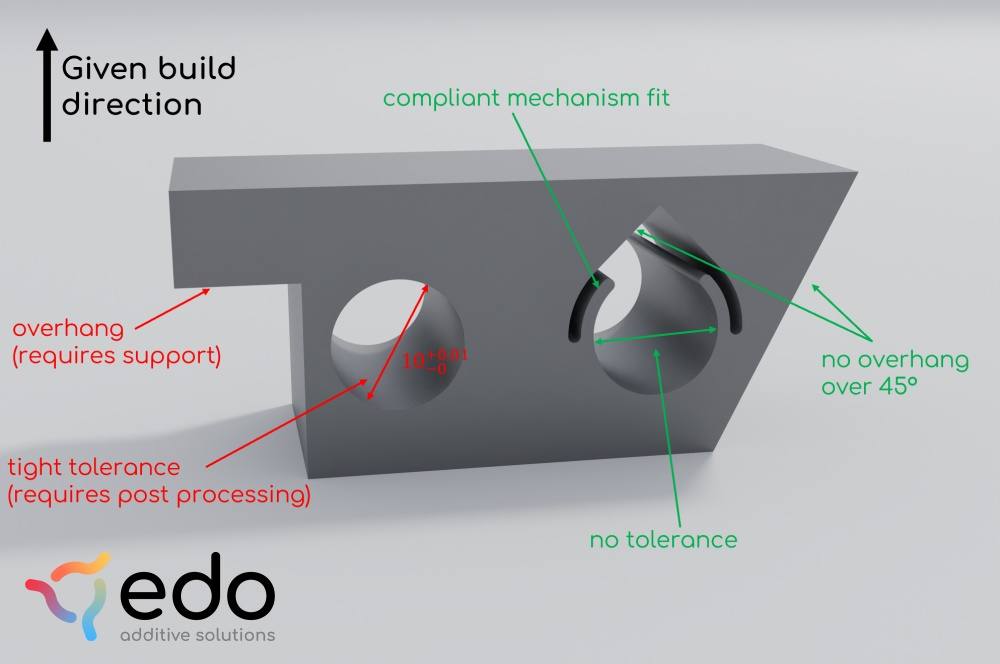
Examples of dos (green) and don’ts (red) in a 3D printed part
3 Avoid uneven mass distribution in parts
Parts that are very solid in one region and very finely structured close by will encounter deformations in many processes. These deformations are usually caused by the generation of heat most processes produce. This issue can often be solved with infills that are not fully dense, lattices or shelling. Sometimes, a change in the printing order can also solve that issue; however, that requires close contact with the machine operator and a good knowledge of what is feasible and what is not.
4 Avoid tight tolerances on geometry, dimensions and surfaces
Tight tolerances are not a strength of most 3d printing processes. This includes geometric dimensional and surface roughness. Tight tolerances in 3D printing most often directly relate to some sort of post-processing like turning, milling or grinding. However, there are many instances where tolerances are not needed in the first place. With 3D printing, it’s possible to print assemblies in place, so assembly tolerances are not needed because the whole assembly is printed in one part. Another strategy to avoid tolerances is compliant mechanisms. For example, in a conventional part, a hole and a pin would both have a tolerance to make a tight fit. In 3D printing, it’s easily possible to create a mechanism in the hole that will comply upon insertion of the pin and, therefore, create a tight fit, entirely without tight tolerances.
5 Avoid poorly accessible cavities
With 3D printing, it’s possible to create very complex cavities, which would traditionally not be possible. However, it is still a good idea to at least leave a 5 mm hole for removal of powder or resin. The larger the hole, the smaller the post-processing efforts will be, which will trickle down to the part price. Some 3D printing technologies do not require a hole at all (for example, FDM) because there is no power or resin to be removed.
6 Think about build orientation in advance
Just because 3D printing has a lot more design freedom than other processes, it still is highly advisable to think about the specific process, its ups and downs and, most importantly, about build orientation. Thinking about the manufacturing process during design can also save a lot of money in AM later on in mass production. However, the nice thing with 3D printing is that if you do not think about all the aspects initially, it’s also not the end of the world because it probably is printable regardless of how complex the design is. Experts can help you in optimising the parts to bring down cost later without the need of creating new moulds or tools. This makes optimising 3D printed parts with the right expertise way easier than their traditional counterparts.
Conclusion
The exact design guidelines depend on the process, manufacturer and material. However, there are some overarching ideas which in most cases hold true and will help reduce part cost. Most of the time these design guidelines try to minimise material and postprocessing labour. However, exploiting the exception to those overarching guidelines will often help to make a part that is not only good but brilliant. This, however, requires a lot of expertise in the field of design manufacturing and a deep understanding of the involved process and materials. Don’t be afraid to start with additive manufacturing, especially because of its ability to optimise parts also in later stages of the product life cycle because there is no mould or tooling required. Therefore, it can help you keep costs low during the development and introduction of a product since it does not need to be optimised to the last cent, and when the product is becoming a success more effort can be put into optimising the part to make it more cost-effective.
We can answer any question about Additive Manufacturing, give courses on AM topics, design your parts and find the right applications for AM in your company. Just give us a call or write us here, and don’t forget to subscribe to our newsletter.
The next releases will cover:
- 3D Printing In-house vs Contract Manufacturing
- How to Find the Right 3D Printing Process
- High-resolution 3D Printing (SLA/DLP)
- Holistic Benefits of 3D Printed Parts
- Low Quantity Parts / Replacement Parts with 3D Printing
Subscribe to our newsletter to learn more about additive manufacturing.