High-resolution 3D Printing (SLA/DLP)
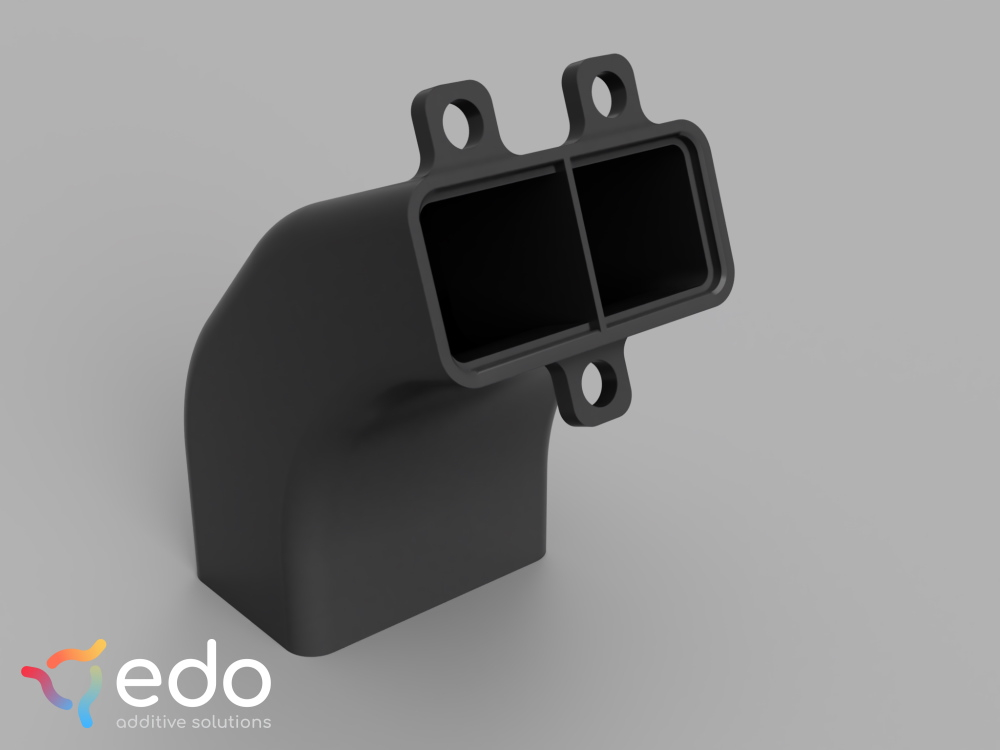
Introduction
There are many different 3d printing technologies that support high resolutions, fine details and smooth surfaces. We will focus on Stereolithography (SLA) and on Digital Light Processing (DLP). They are both widespread and highly developed 3D printing technologies that range from cheap hobby machines to large industrial machines and can print a wide variety of polymers. However, the learnings from this article apply to many similar other technologies (e.g. LCD-based printers, CLIP, etc.) as well.
The technology
SLA and DLP 3D printers are based on light-sensitive resins that go from liquid to solid when hit by light. The main difference between SLA and DLP 3D printing is in the way how these light-sensitive resins are activated and therefore polymerize. SLA 3D printers use a laser with a single spot, while the DLP’s illuminate the entire layer at once, similar to a cinema projector. Usually, the spot/pixel size, which defines the maximum resolution, is between 40 and 120 um (however, it can go down to 2 um). There are also differences in the layout of the light source and the vat in which the resin is stored between different printers. Usually, they are split into top-down and bottom-up systems. Both layouts have their advantages and drawbacks.
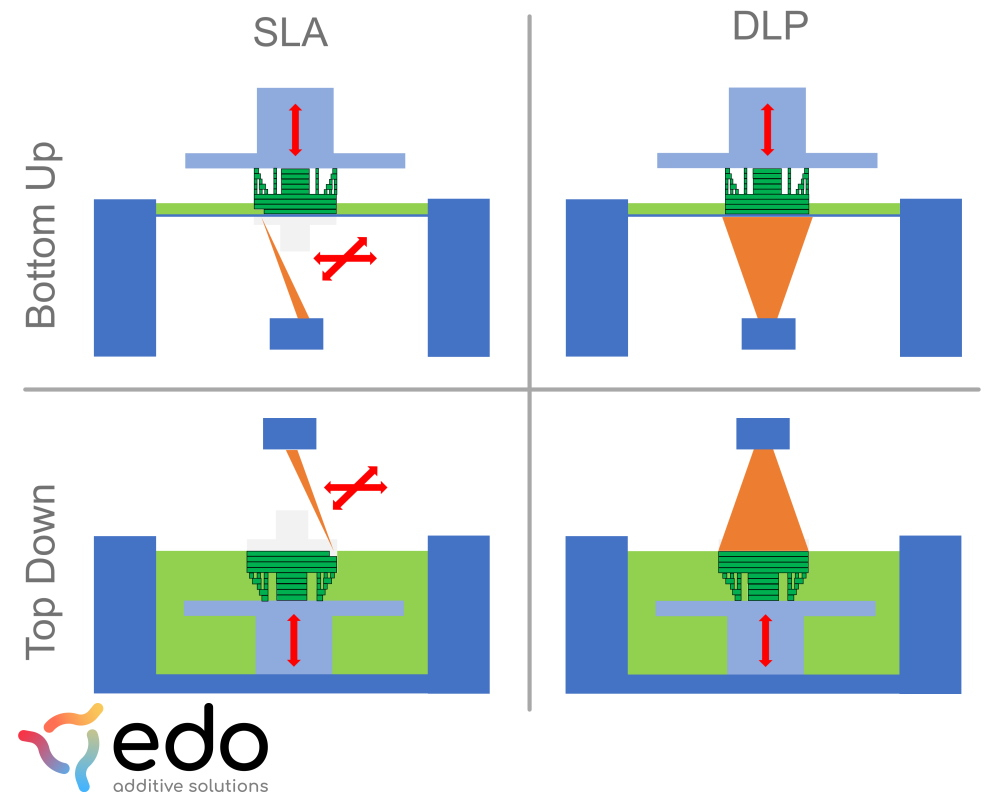
Working principle of SLA/DLP 3D printing: A light source hardens a polymeric resin selectively at all points that should be part of the final geometry.
Strengths & Weaknesses
Overall, SLA and DLP printers are excellent at printing high-resolution polymer parts. They, however, require support structures which inturn can leave behind marks and need time to remove. SLA and DLP printers are well-developed machines suitable for mass production in industrial settings. However, there are subtle differences between SLA and DLP as well as top-down and bottom-up:
SLA (Stereolithography):
SLA 3D printing tends to be slower than DLP because the layers are not cured at once, however SLA 3D printers can be larger in build volume while maintaining the same resolution. The movement of the laser means that there are also no pixels and therefore, rounded parts can be smoother.
DLP (Digital Light Processing):
DLP 3D printers are limited in their size by the resolution needed. That is because the optics are only available up to a certain amount of pixels (current maximum 4096×2176 Pixel, at e.g. 50 um pixel size, this would be a maximum part size of 204 mm x 108 mm). However, they are usually faster.
Top Down
Usually, the forces acting on the part are smaller since there is no detaching from the window required after each layer. This can reduce part deformations and support needs. Usually top-down machines also require less maintenance since there are no consumables like windows which need to be replaced regularly. More unconsumed resin is usually needed while printing because the whole vat needs to be filled with resin. As some resins are up to $500/l, this can make prints more expensive.
Bottom Up
Bottom-up systems tend to be more compact in size. However they are also usually smaller in build volume. Bottom-up 3D printers usually have a more efficient resin system in the sense that more of the used resin is actually used and does not stay in the vat.
Applications
There are many different industrial applications of resin 3d printing, we tried to list some of the most important here:
Data Visualisations
By converting large amounts of numerical information into physical models, businesses and researchers can enhance their understanding of data patterns. This enables their external and internal customers to physically interact with the visual representation, fostering a deeper comprehension of the information at hand. From architectural models to anatomical representations, SLA 3D printing transforms abstract data into tangible, comprehensible information.
Visual Prototypes
One of the most prominent applications of SLA 3D printing lies in the rapid and precise prototyping of designs. Whether in product development, industrial design, or architecture, SLA technology allows for the creation of highly detailed and accurate visual prototypes. This capability significantly accelerates the product development cycle, enabling designers to assess the look, feel, and functionality of their creations with unparalleled precision. The iterative nature of SLA 3D printing empowers designers to make quick adjustments and refinements, ultimately leading to more robust and innovative final products.
Everything small and detailed
SLA 3D printing excels in producing small and intricate objects with high precision, making it the preferred technology for creating intricate jewellery, dental models, and micro-scale components. This application has opened up new possibilities in industries where intricate and delicate designs are paramount, allowing for the production of highly detailed objects that would be challenging or impossible to create using other manufacturing techniques.
Functional Mechanical parts
By Utilising resins with specific mechanical properties, such as toughness and impact resistance, SLA can now produce components that meet the requirements for functional prototypes and end-use parts. This application is particularly valuable in industries like aerospace and automotive, where the need for lightweight yet durable components is critical. The ability to produce custom, complex geometries with high precision makes SLA 3D printing a versatile solution for creating mechanically robust parts.
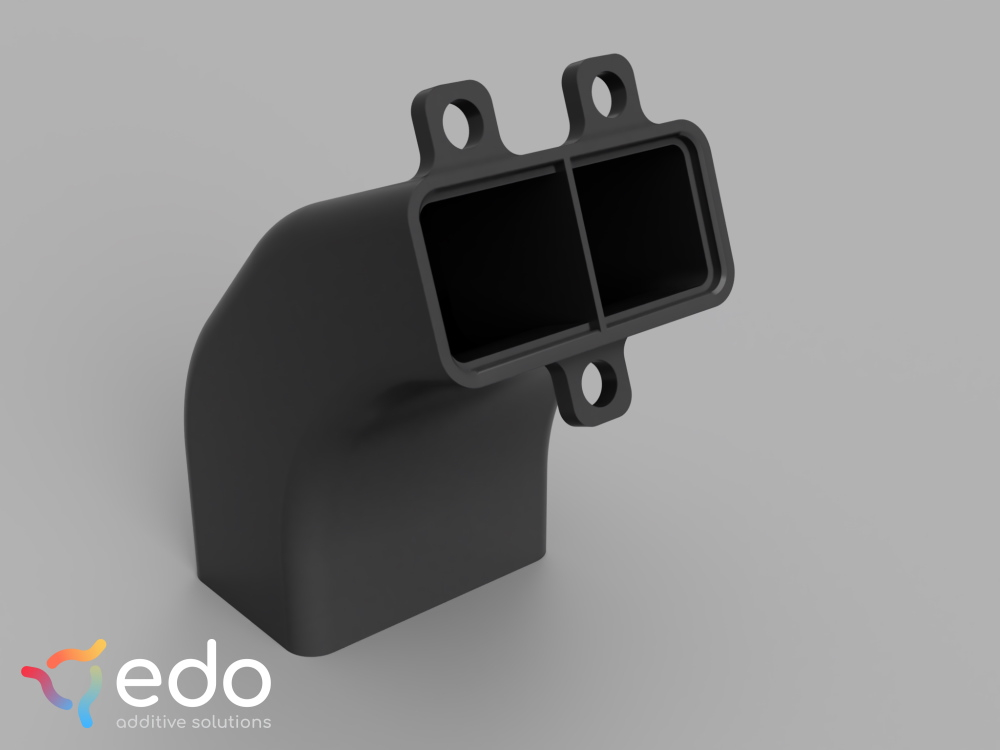
An industrial air duct printed with a high-temperature SLA resin. SLA creates a very smooth surface which can help for better airflow.
Conclusion
SLA and DLP 3D printing are both capable systems with usually high resolutions. Both technologies are very mature and widely used in industry. In the end, the specific 3D printer needs to fit your needs, therefore, it is often not that relevant which exact technology is used but what resolution is required, what material is needed and what the print speed and size should be.
We are the experts to support you with exactly these questions about additive manufacturing. Just give us a call or write us here.
The next releases of our newsletter will cover:
- Holistic Benefits of 3D Printed Parts
- Low Quantity Parts / Replacement Parts with 3D Printing
- 3D Printed Waveguides
- Replacing Moulded Parts with 3D Printed Parts
- How to Minimise the Cost of 3D Prints
Subscribe to our newsletter to learn more about additive manufacturing.