Support-free 3D printing with SLS/MJF
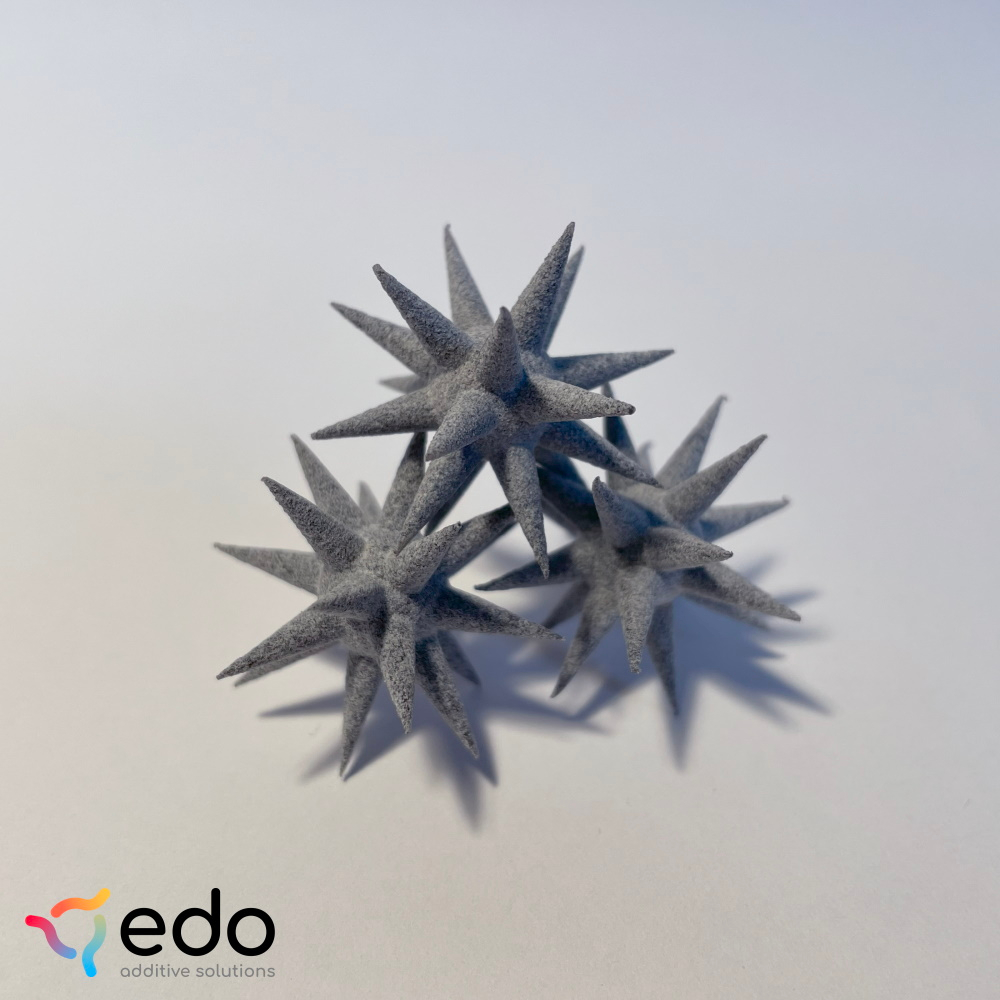
Introduction
Complete design freedom is one of the most significant advantages of 3D printing. However, you might have heard of limiting factors like support structures, minimum overhang angle, or build orientation. These concepts originate from additive processes that are incapable of printing in thin air.
Selective Laser Sintering (SLS) and Multi Jet Fusion (MJF) are different technologies that have a lot in common. Technically, both use support structures, namely the powder bed the parts are printed in. However, since the powder bed is not physically attached to the part, it can be brushed away easily after printing. That enables a degree of design freedom most often unmatched by other technologies.
How does SLS/MJF work?
SLS and MJF are both additive manufacturing technologies that construct three-dimensional objects layer by layer inside a powder bed, which serves as support and raw material. The building process involves the selective application of energy to specific regions to melt the raw powder into a part. In SLS, a high-power laser selectively fuses the powder. In MJF, a liquid agent is deposited onto the powder bed and then fused using infrared light.
Overall, both SLS and MJF have similar capabilities in terms of resolution, minimum feature sizes, and surface roughness. Both feature tighter tolerances than other processes like FDM 3d printing.
SLS is versatile, accommodating a range of materials such as polymers, metals, and ceramics. On the other hand, MJF is particularly adept at working with nylon-based materials, which, compared to SLS, can come in multicolor and deliver parts with commendable strength and flexibility.
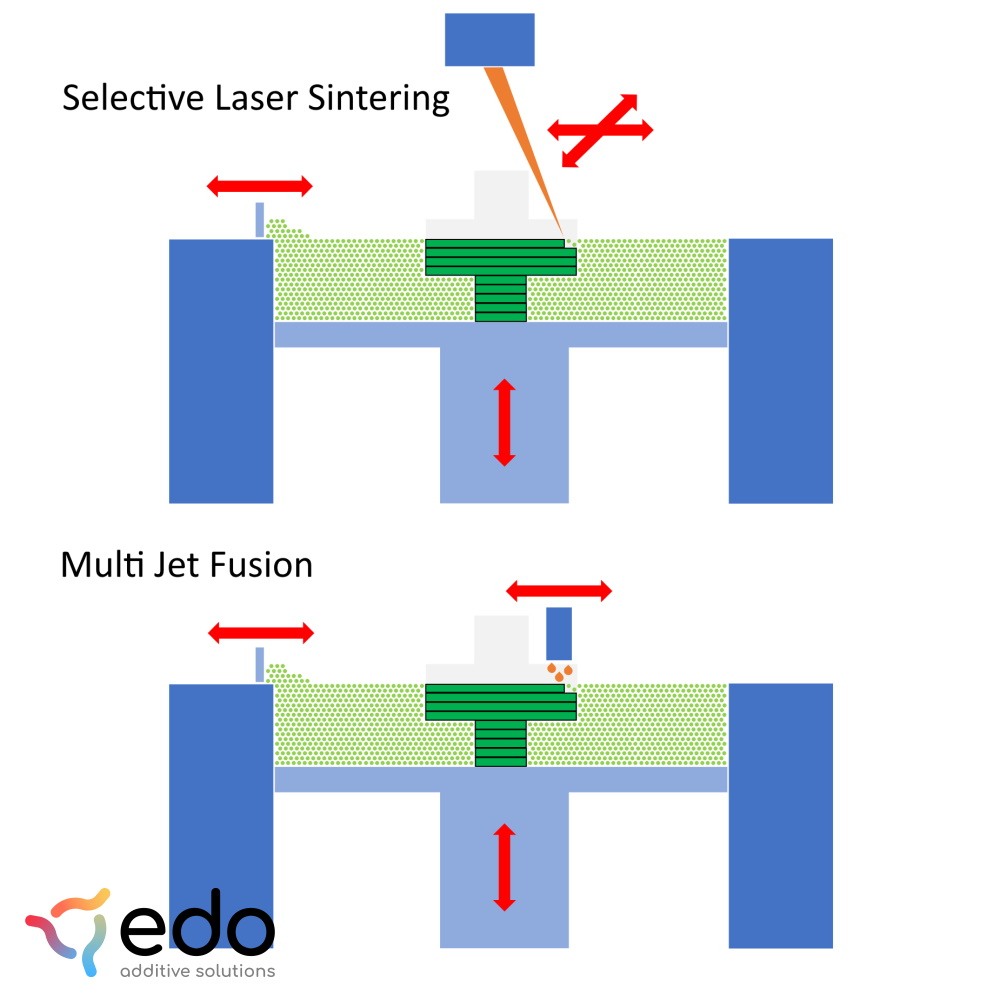
Schematic working principle of SLS and MJF
What is the advantage of that additional design freedom?
With the gained design freedom, the designer is not limited anymore to thinking about building orientation and overhangs. There is no need to consider the placement and removal of support structures. In the end, this means that the designer of the part can entirely focus on the design of the part without thinking about how it is manufactured. This can help engineers design better parts. There are only two major limitations: The materials and the fact that cavities need to be minimally accessible so that the powder can come out of the part. Since it is a powder, a 5mm large hole for a randomly shaped cavity is usually enough. This gained design freedom allows for undercuts, lattice and gyroid structures, cooling channels, and complete print-in-place assemblies, which would not be possible with traditional machining and often not even possible or extremely difficult with other additive manufacturing technologies.
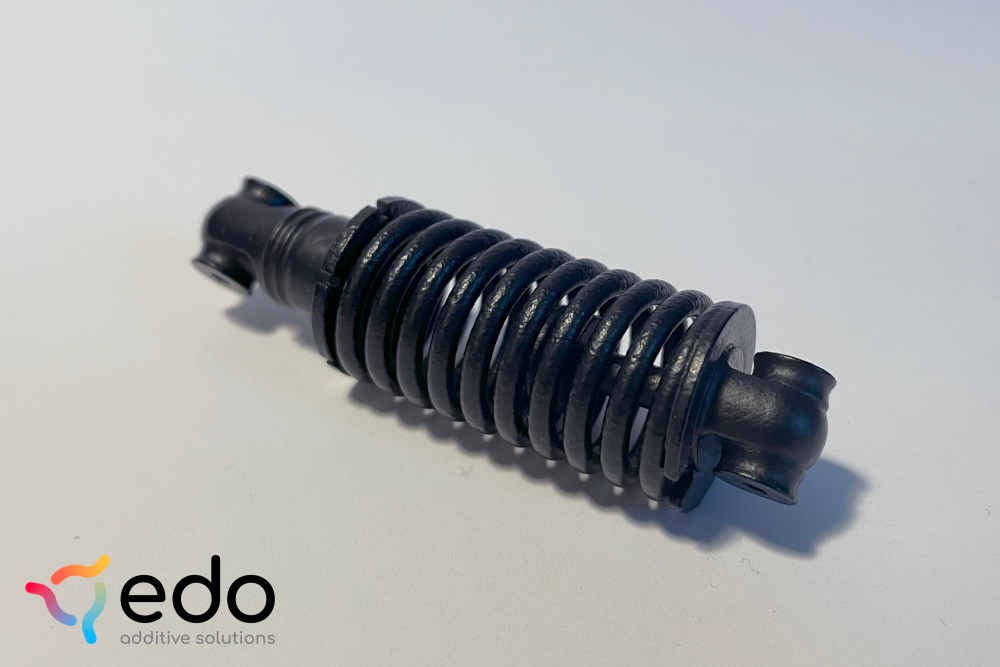
Example of a conventionally complex assembly printed in a single MJF Part
Which system is the right one for me?
It comes down to your application, budget, preferences, and future use cases. In summary:
- Process: SLS utilizes a high-power laser to selectively sinter powdered material, while MJF employs liquid agents selectively deposited onto a powder bed and fused using infrared light.
- Materials: SLS is versatile, accommodating a variety of materials, including polymers, metals, and ceramics. In contrast, MJF is primarily used with nylon-based materials, which might be multi-color.
- Precision: Both processes are similarly precise and, therefore, allow for similar minimum feature sizes and details. Also, the surface roughness of both processes is similar; there might be differences for specific machines.
Advantages of SLS and MJF compared to other technologies:
- Versatility in material selection
- Ability to produce intricate designs without support structures
- High precision and speed
- Capable of producing strong and flexible parts, especially with nylon-based materials
Disadvantages of SLS and MJF compared to other technologies:
- Longer production times compared to some other 3D printing methods
- Powder might be difficult to remove from internal geometries
- Surface finish may require post-processing for specific applications, quite rough finish compared to other technologies.
- Limited material options with MJF
- Initial equipment costs may be higher
Conclusion
SLS and MJF are compelling technologies that have their place in the additive landscape. They are similar at first glance in what they produce. However, they are still different in what they can achieve and what their ideal use case is. Nevertheless, both technologies can be considered one of the most versatile manufacturing processes humanity knows. It’s the closest we have yet to the magic all-manufacturing production machine out of movies.
If you are still trying to figure out if you need all that flexibility or are uncertain if that flexibility comes at a too high cost in terms of speed, material selection, or price for your application, we help you find the best process for your application.
Regardless of whether you have already chosen what technology to use or not, consider optimizing your parts for additive manufacturing to maximize your investment. We help you to get that last bit of efficiency out of your part or design it from scratch. Call or write us here, and we will find the best solution to your difficulties!
The next releases will cover:
- Additive Manufacturing for Robotics
- Metal 3D Printing with Laser Powder Bed Fusion (LPBF)
- Weight Reductions with 3D Printing
- 3D Printing of Aluminum Alloys
- Lattice Structures and their Applications
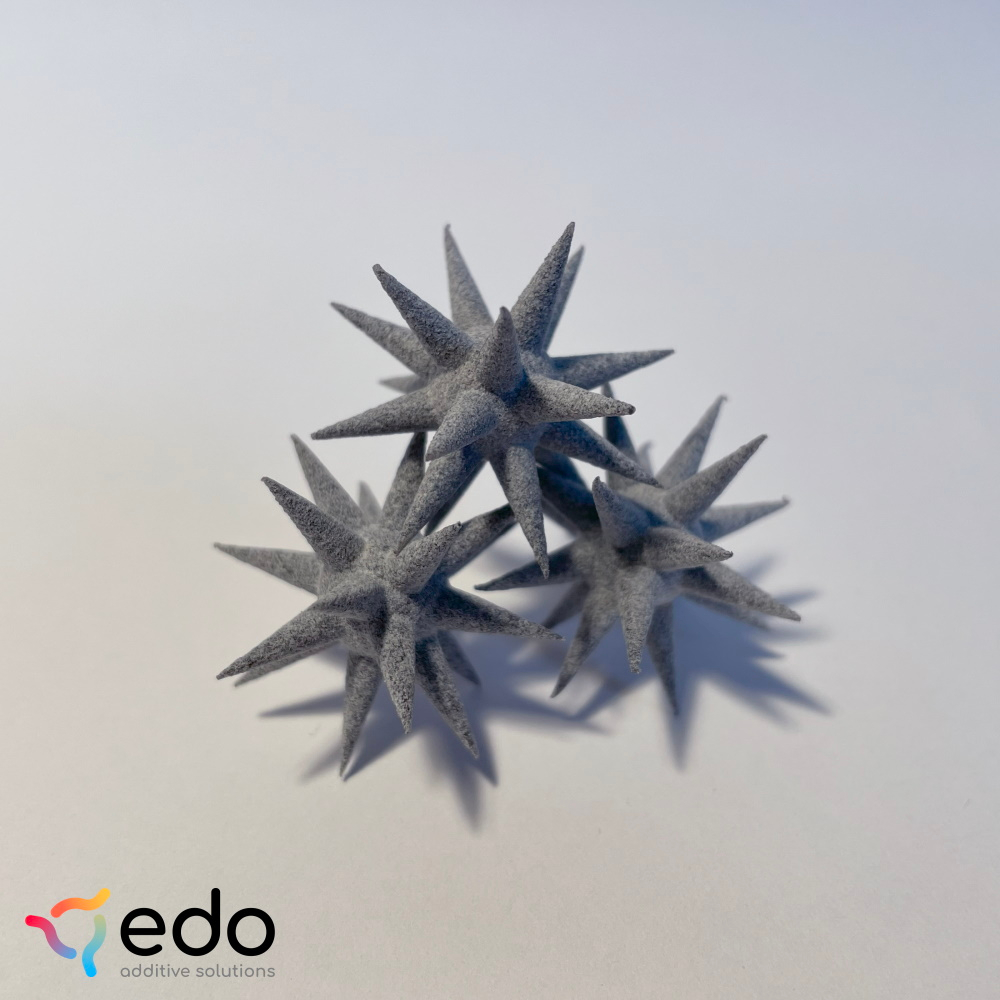
MJF part with sharp spikes shows the possibility to print complex structures without support
Subscribe to our newsletter to learn more about additive manufacturing.