Metal 3D Printing with Laser Powder Bed Fusion (LPBF)
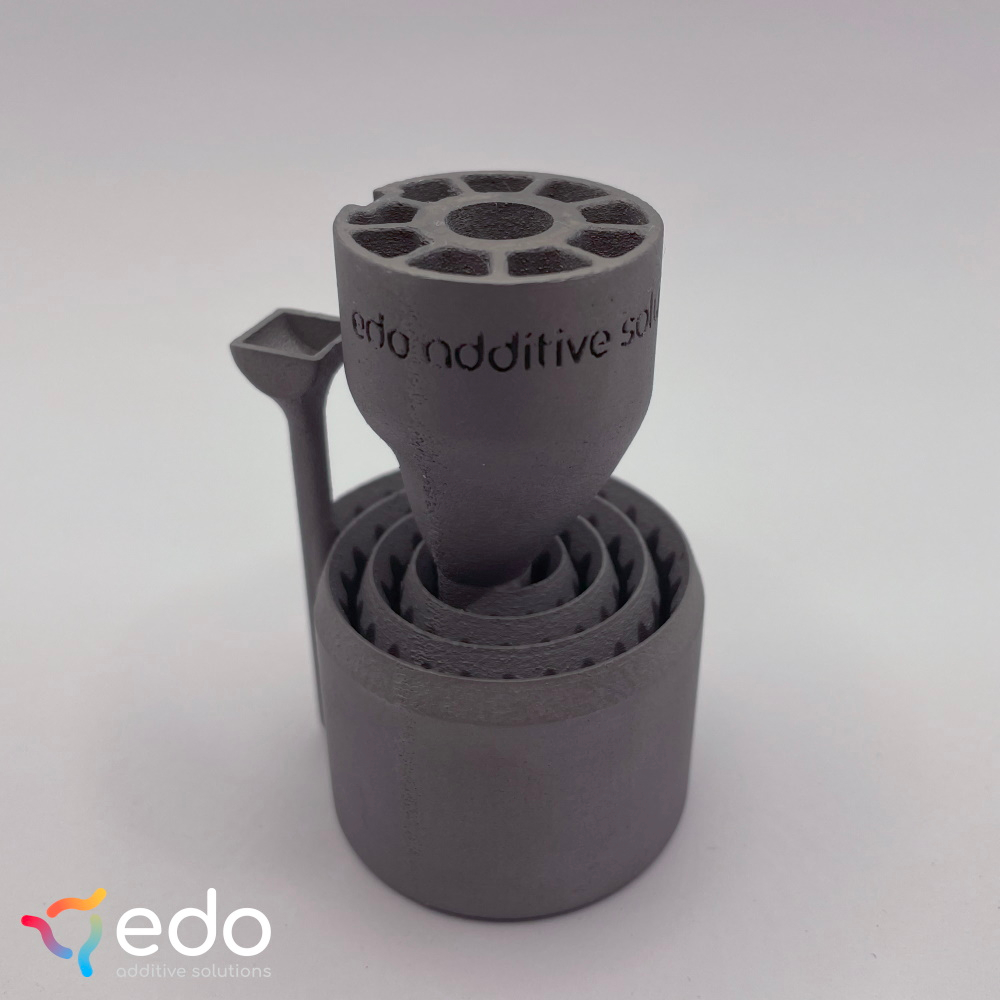
Introduction
Metals have been processed and used for thousands of years for their unmatched properties in almost all thinkable applications. However, while the bulk properties of metals are excellent, a lot of potential is wasted due to constraints in manufacturability of more complex geometries. This becomes especially apparent in performance-sensitive applications where parts should be highly optimized and must deliver top performance.
3D printing is the perfect technology to enable bridging this gap. So how does it do this?
Metal 3D printing – Laser Powder Bed Fusion
There are many different technologies on the market to print metal parts. We will focus on the most common technology in metal 3D printing, called Laser Powder Bed Fusion (LPBF).
Conceptually, it is similar to SLS polymer 3d printing. Metal powder is spread in thin layers (usually 30µm – 200µm) and selectively melted with a high-power laser source (ranging from 100W to 2000W).
LPBF and SLS mainly differ in the materials processed and the fact that LPBF requires support for conducting the thermal energy away and avoiding warping of the parts caused by the high amounts of energy needed for the metal to melt. These supports must be removed after the printing is done.
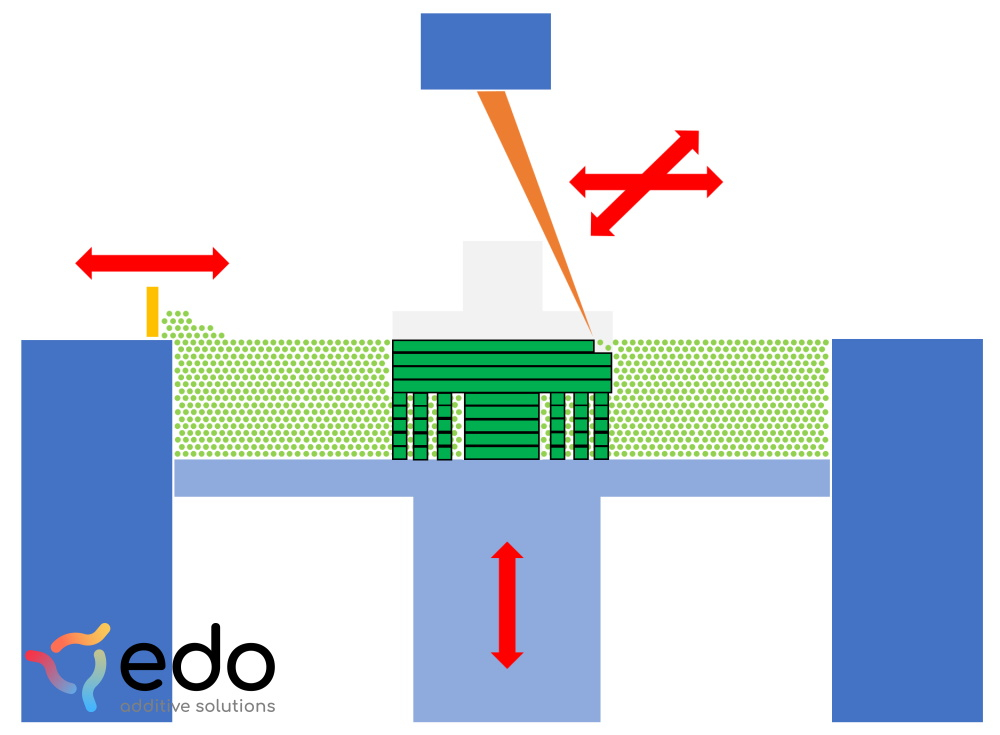
Conceptual visualization of the LPBF process. The support structures, the powderbed, and the high-power laser are clearly visible.
Advantages and Disadvantages
The advantages of metal 3D printing with LPBF are the strong material properties of metals and the great availability of the process itself. Parts made out of metal bring the advantage of recyclability, heat resistance, high strength, durability and, in some applications also their higher density.
Because LPBF is so widespread, the parts are less expensive than parts made with other metal 3D printing technologies. However, the cost per part will still be higher than the cost of an identical polymeric part made with FDM, SLS or resin.
Usually, parts produced with LPBF need some sort of post-processing. This often includes support removal, sometimes also milling surfaces and general surface treatment like bead blasting or sanding to reduce the surface roughness. Faces that require tolerances for gaskets, bearings, or similar need to be post-processed with milling because LPBF can not produce very tight tolerances. This however can increase cost and lead times.
While Interlocking parts and print-in-place assemblies are difficult to achieve with LPBF, it really shines when it comes to complex geometries and compliant mechanisms (see our 3D printed Manometer).
There are more advanced additive manufacturing technologies that do not require as extensive support and post-processing as LPBF does and, therefore enable more design freedom. However, they are usually quite limited in the range of materials, availability and competitiveness of cost.
Applications
Metal 3d printing is useful everywhere where complex geometries, mass customization, compliant mechanisms or top performance are required.
One primary application of metal 3D printing is in the aerospace industry. It allows for the production of lightweight, intricate components like brackets, heat exchangers, cooling systems and rocket nozzles that traditional manufacturing methods struggle to achieve. Aircraft manufacturers utilize this technology to fabricate parts with reduced weight, enhancing fuel efficiency while maintaining structural integrity.
In the medical field, metal 3D printing plays a crucial role in producing custom implants and prosthetics. It enables the creation of patient-specific implants tailored to individual anatomies, improving patient outcomes and reducing surgery time.
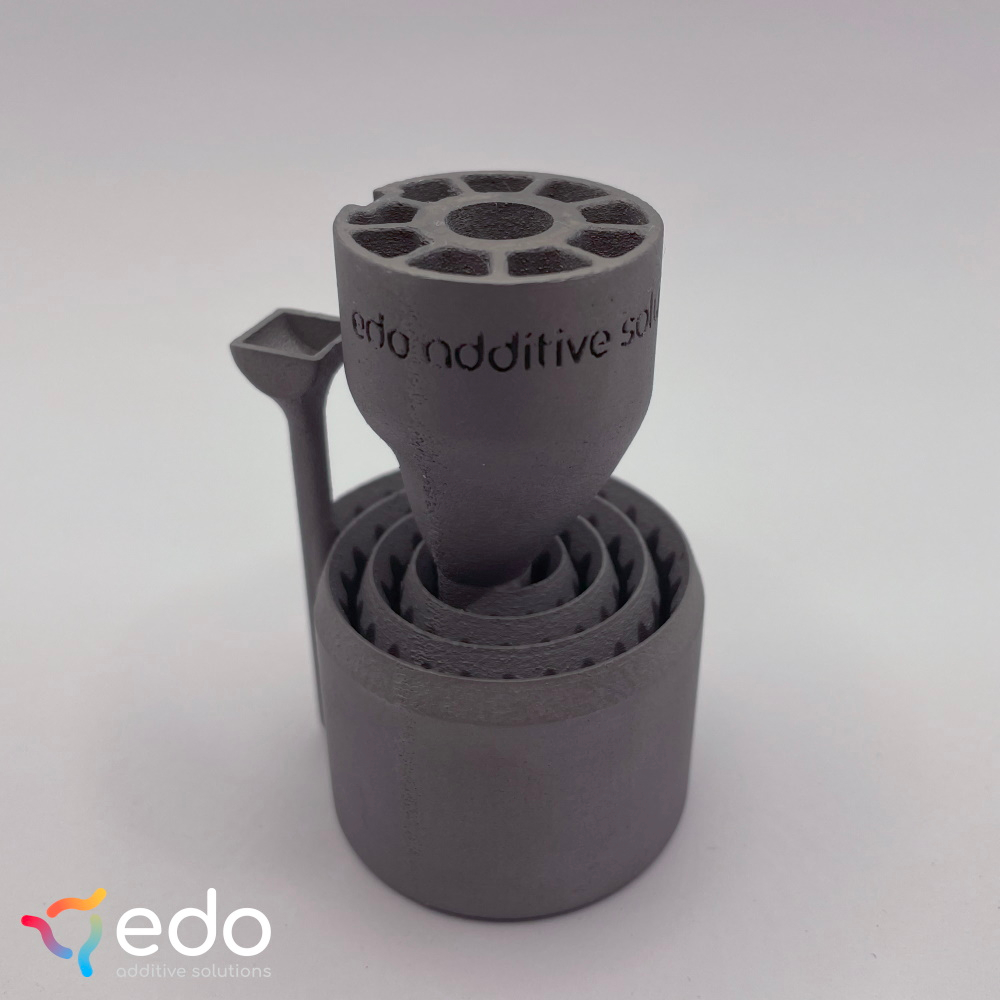
LPBF 3D printed compliant mechanism (see Projects)
Conclusion
LPBF enables a completely new set of material properties in additive manufacturing. Metal 3D printed parts can be used in many industries and can enhance the performance of parts. However, operating LPBF machines is comparably complicated; designers need to consider the printing process, and it’s important to remember that it’s a more expensive process than most polymer 3D printing processes. However, with sound design strategies, the proper application and the usage of metal 3D printing, it can become a true cost-saver and product improver.
We help you determine if metal 3D printing is the right technology and design your parts to be technically and economically feasible. Give us a call or write us here.
The next releases will cover:
- Weight Reductions with 3D printing
- 3D Printing of Aluminum Alloys
- Lattice Structures and their Applications
- Essential Design Rules for Mass 3D Printing
- 3D Printing In-house vs Contract Manufacturing
Subscribe to our newsletter to learn more about additive manufacturing.